The Ultimate Guide to Choosing a Plastic Mold Supplier
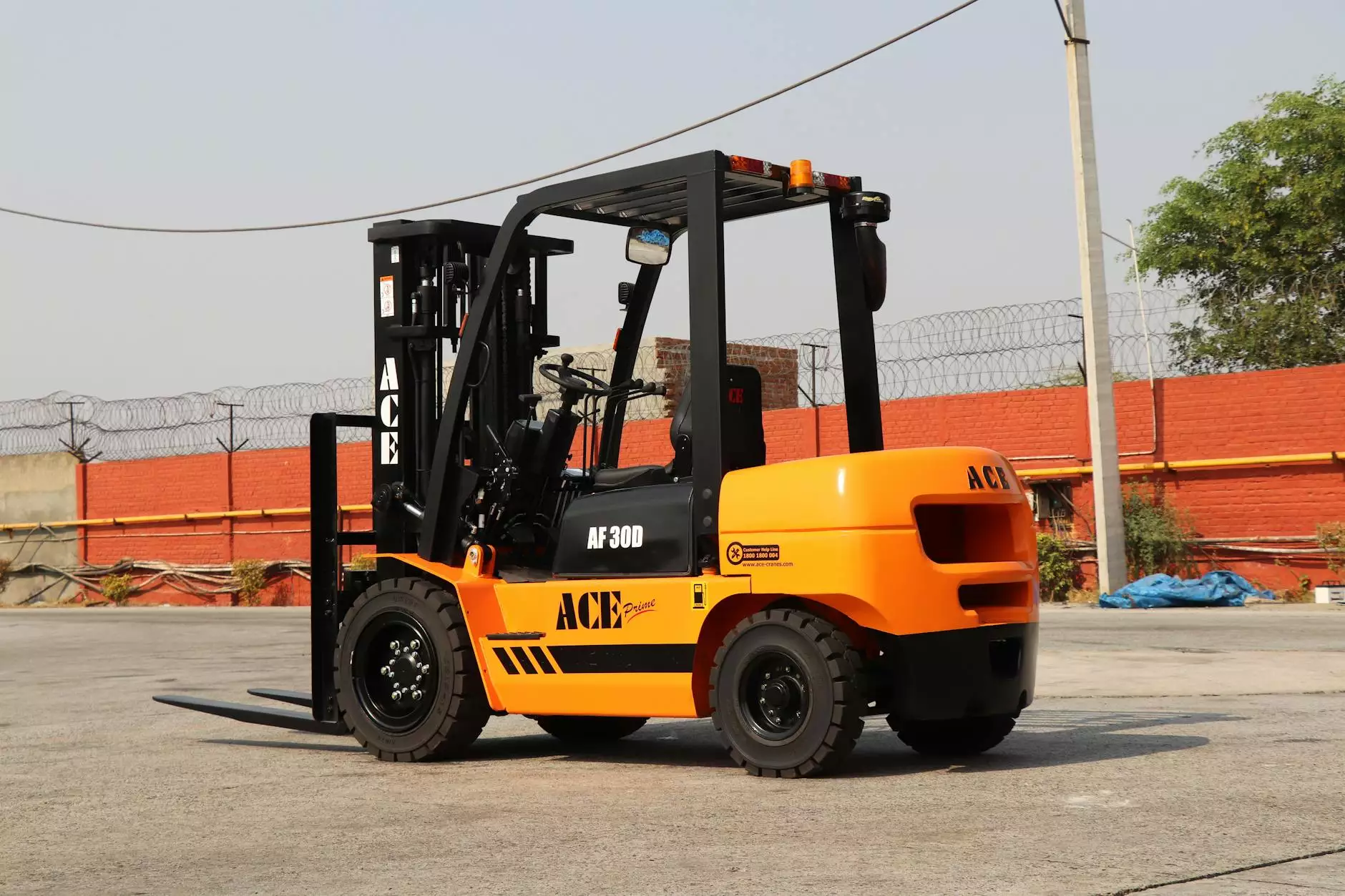
In the vast world of manufacturing, the choice of a plastic mold supplier is a critical decision that can significantly impact your production efficiency, product quality, and overall business success. This guide aims to provide comprehensive insights into the various aspects of selecting the right supplier, ensuring you make an informed choice that aligns with your business needs.
Understanding the Role of a Plastic Mold Supplier
A plastic mold supplier is a company that specializes in designing, manufacturing, and supplying molds that are used for plastic injection molding processes. These molds are essential for producing plastic parts across various industries, including automotive, consumer goods, electronics, and medical devices. The quality and precision of the mold directly affect the final product's strength, durability, and functionality.
Why Choose a Reliable Supplier?
Choosing a competent supplier ensures several benefits:
- Quality Assurance: Reliable suppliers maintain rigorous quality control processes to ensure that molds are manufactured to precise specifications.
- Timely Delivery: A dependable supplier can provide a consistent supply of molds, thus minimizing downtime in production.
- Technical Expertise: Experienced suppliers offer valuable advice and support in mold design and production, helping you achieve optimal results.
- Cost-Effectiveness: By collaborating with a skilled supplier, you can reduce the total cost of ownership through efficient mold designs and manufacturing processes.
Key Factors to Consider When Selecting a Plastic Mold Supplier
When evaluating potential plastic mold suppliers, consider the following critical factors:
1. Expertise and Experience
Assess the supplier’s background in mold manufacturing and their experience in your specific industry. A supplier with extensive experience is likely to have encountered various challenges and developed effective solutions over time.
2. Portfolio of Work
Review the supplier's previous projects to evaluate the quality of their work. A robust portfolio showcasing diverse mold designs and applications can provide insights into their capabilities.
3. Technical Capabilities
Ensure that the supplier has advanced technology and equipment for mold design and manufacturing. This includes:
- CAD/CAM Software: Advanced design software allows for precise mold designs and simulations.
- CNC Machining: Computer Numerical Control (CNC) machining ensures high accuracy in mold manufacturing.
- Additive Manufacturing: 3D printing technology can be beneficial for creating complex mold geometries.
4. Customer Support and Communication
Effective communication and strong customer support are vital when working with a plastic mold supplier. Ensure that they are responsive and willing to assist you throughout the design and production process.
5. Cost Structure
While cost should not be the only factor, it is essential to understand the supplier's pricing model. Look for transparency in pricing and inquire about any additional fees for design alterations, maintenance, or warranty services.
The Process of Working with a Plastic Mold Supplier
Understanding the workflow when collaborating with a plastic mold supplier can help streamline the project:
1. Initial Consultation
Begin with an initial consultation to discuss your project requirements. Clearly communicate your expectations regarding mold design, material specifications, and production timelines.
2. Design Phase
The supplier will create detailed mold designs based on your specifications. During this phase, you may review and request revisions until the design meets your satisfaction.
3. Prototyping
Many suppliers offer prototyping services, allowing you to evaluate the mold’s design before full-scale production. This step is crucial in identifying potential issues early on.
4. Production
Once approved, the supplier will proceed with mold manufacturing. Regular updates during this phase will keep you informed about progress and lead times.
5. Testing and Quality Assurance
Upon completion, the molds will undergo rigorous testing to ensure they meet quality standards and operational requirements. This phase may include trial runs using the molds to produce test parts.
Maintaining a Successful Relationship with Your Supplier
Building a strong partnership with your plastic mold supplier is essential for long-term success. Here are some tips to foster a positive working relationship:
- Clear Communication: Maintain open lines of communication to address any concerns, changes in requirements, or feedback promptly.
- Set Mutual Goals: Share your business objectives and collaborate on achieving them, ensuring both parties benefit from a successful partnership.
- Provide Constructive Feedback: Offer feedback on the molds and services provided, as this can help the supplier improve and adapt to your needs.
- Establish Long-Term Contracts: Consider entering into long-term agreements which can yield cost savings and ensure priority service.
Conclusion
In conclusion, choosing the right plastic mold supplier is a strategic decision that requires careful consideration of various factors including experience, technical capabilities, and communication. By following the guidelines provided in this article, you can make informed decisions that lead to successful manufacturing outcomes, ensuring the quality and efficiency of your products. Partnering with a reliable supplier like Deep Mould can provide you with the assurance of high-quality molds tailored to your specific needs. Remember, investing time in selecting the right supplier can pay dividends in the long run, both in terms of cost savings and product excellence.