Understanding Die Casting Parts Manufacturers: A Comprehensive Guide
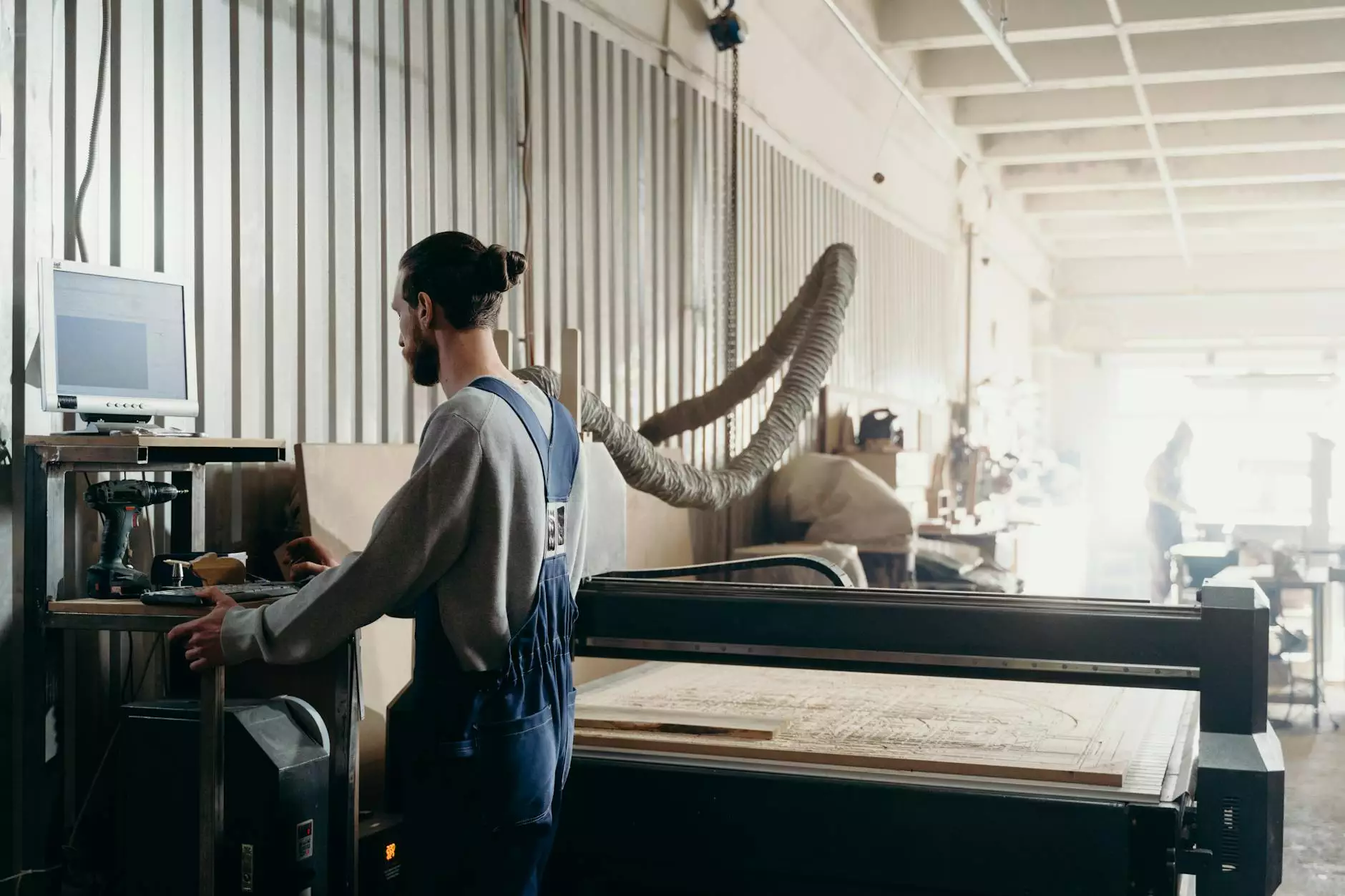
In the realm of manufacturing, the term die casting parts manufacturers resonates deeply across various industries. These manufacturers are vital players in producing high-quality metal parts that meet rigorous standards. In this article, we will delve into the intricacies of die casting, shed light on the capabilities of manufacturers, and explore their significance in today's economy.
What is Die Casting?
Die casting is a precision manufacturing process that involves forcing molten metal into a mold cavity under high pressure. This technique allows for the production of complex shapes with intricate details. The most commonly used materials in die casting are aluminum, zinc, and magnesium due to their lightweight properties and resistance to corrosion.
The Die Casting Process
The die casting process involves several crucial steps:
- Melting the Metal: The selected metal is melted in a furnace until it reaches the appropriate temperature.
- Injecting the Metal: The molten metal is injected into a steel mold at high pressure, allowing it to fill all cavities.
- Cooling: Once injected, the metal cools and solidifies, taking the shape of the mold.
- Removing the Casting: After cooling, the mold is opened, and the casting is ejected.
- Finishing Processes: The castings may undergo further processes such as machining, surface treatment, or polishing, depending on the required specifications.
The Role of Die Casting Parts Manufacturers
The importance of die casting parts manufacturers cannot be overstated. They are responsible for not only creating parts but also ensuring that these parts meet quality standards, industry specifications, and customer demands. Here’s how manufacturers contribute to various sectors:
Industries Served by Die Casting Manufacturers
Die casting parts find applications in a multitude of industries, including:
- Aerospace: Precision components for aircraft engines, fuselage parts, and structural elements.
- Automotive: Engine blocks, transmission cases, and radiator housings are typical products of die casting.
- Electronics: Housings for smartphones, tablets, and other electronic devices are often die cast.
- Consumer Goods: Appliances, furniture hardware, and tools.
- Medical Devices: Equipment such as surgical instruments and diagnostics devices rely on die casting for reliability and precision.
Benefits of Choosing Die Casting
Manufacturers and consumers alike benefit from the die casting process. Here are some of the key advantages:
1. High Precision and Dimensional Accuracy
One of the defining features of die casting is its ability to produce parts with exceptional precision. The manufacturing process ensures that parts are made to exact specifications, reducing the need for extensive finishing processes.
2. Cost-Effectiveness for High Volumes
Although the initial setup cost for die casting can be high due to the required molds, the scalability of the process allows manufacturers to produce large quantities at a lower per-unit cost. This is particularly beneficial for mass production runs.
3. Exceptional Strength and Durability
The materials used in die casting, particularly metals, provide parts with outstanding mechanical properties. Die-cast components are typically stronger and more durable than those manufactured through other methods, which is essential for critical applications.
4. Complex Shapes and Designs
Die casting allows for the production of complex geometries that would be challenging to achieve with traditional manufacturing methods. This capability makes it a preferred choice for product designers looking to innovate and create efficient designs.
Choosing the Right Die Casting Parts Manufacturer
Selecting the right die casting parts manufacturer is a crucial decision for any business. Here are some factors to consider when making your choice:
1. Industry Experience
Look for manufacturers with extensive experience in your industry. Their knowledge of specific requirements, regulations, and design considerations can significantly benefit your project.
2. Quality Assurance Practices
The best manufacturers implement rigorous quality control processes. Inquire about certifications such as ISO 9001, which demonstrate a commitment to quality management.
3. Technological Capabilities
The die casting industry is continually evolving, and top manufacturers invest in the latest technology. Assess their capabilities regarding machine types, tooling, and automation to ensure they can meet your needs effectively.
4. Customer Support
Strong customer support is critical for a successful partnership. Choose manufacturers that offer collaborative design assistance, timely communication, and reliable service throughout the production process.
Future Trends in Die Casting
The future of die casting is promising, driven by advancements in technology and changing market demands. Here are some emerging trends to watch for in the industry:
1. Increased Automation
Automation in the die casting process is expected to rise. Smart factories utilizing robotics and AI will streamline production, reduce lead times, and enhance efficiency.
2. Sustainable Practices
As environmental concerns grow, die casting manufacturers are looking for ways to reduce waste and increase energy efficiency. Sustainable practices will not only meet regulatory requirements but also appeal to environmentally conscious consumers.
3. Lightweight Materials
The demand for lighter yet strong materials, particularly in the automotive and aerospace sectors, is driving innovation in die casting. Manufacturers are exploring new materials and alloy combinations to enhance performance and reduce weight.
4. Advanced Design Software
The use of advanced simulation software enables manufacturers to enhance their designs before the actual production begins. This technology minimizes errors and optimizes the die casting process.
Conclusion
The contributions of die casting parts manufacturers to various industries are invaluable. Through precision manufacturing processes, they play a pivotal role in meeting the demands of an ever-evolving market. By understanding the advantages of die casting, the selection criteria for manufacturers, and the current trends, businesses can make informed decisions that enhance their productivity and profitability.
Whether you are an OEM or an engineering firm, partnering with a reliable die casting manufacturer can lead to innovations that propel your projects to success. Explore potential partnerships, invest in quality, and leverage the benefits of die casting to stay competitive in your industry.